admin | Publié le |
Industrie du Futur : Difficile de ne pas céder au 4.0
La 4e révolution industrielle bouleverse les façons de produire, modifie les modes d’organisation et entraîne un changement de culture. Les technologies du 4.0 repoussent les limites du possible dès la conception d’un produit jusqu’à sa réalisation. Pour les entrepreneurs, la tentation est grande aujourd’hui d’investir massivement pour accroître la compétitivité, d’autant plus que le discours ambiant encourage vivement à le faire.
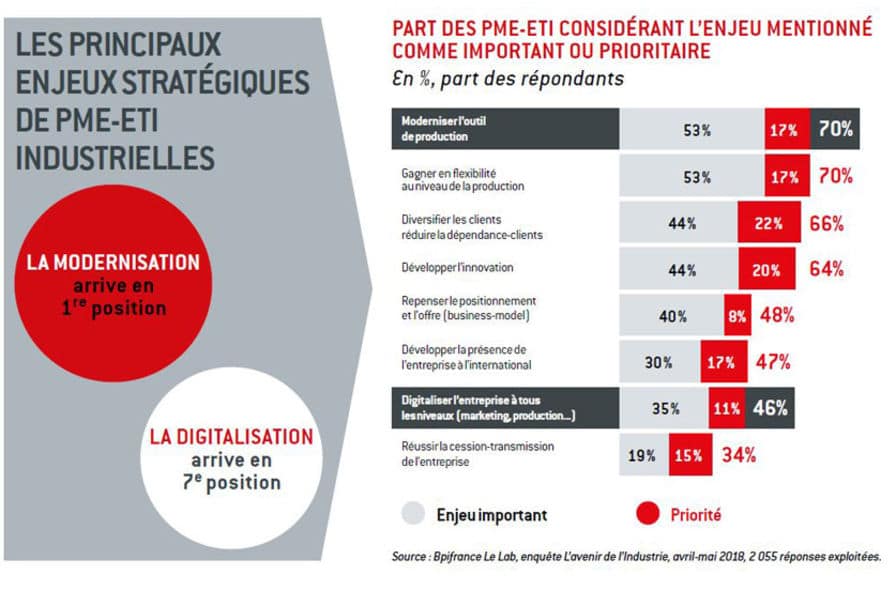
Pour une majorité de cadres et dirigeants industriels, les piliers de l’Usine du Futur combinant le numérique, la robotique collaborative, l’Intelligence Artificielle (IA), la fabrication additive (FA), la réalité étendue, la blockchain, l’IoT (Internet des Objets) sont les leviers qui leur permettront de réduire les coûts, rendre flexible l’outil de production, gagner en agilité, personnaliser les produits en fonction de la demande et satisfaire les consommateurs. Pour bon nombre, il suffit d’investir dans les moyens intégrant les outils du Smart Factory pour pouvoir atteindre les objectifs de performance.
Un engouement des dirigeants pour le 4.0
Ainsi, selon le dernier baromètre de l’Industrie 4.0 réalisé par GFI en partenariat avec OpinionWay et BFM Business auprès d’un échantillon de 200 dirigeants d’entreprises industrielles de 100 salariés et plus, l’industrie 4.0 est vue positivement par l’industrie française (57 %) et comme une bonne opportunité pour sa propre industrie (56 %). Pour 68 % des entreprises interrogées, la transformation digitale est un moyen d’augmenter la productivité et d’atteindre l’excellence opérationnelle.
« L’industrie 4.0 est plébiscitée par les dirigeants, il y a un engouement certain qui ne demande qu’à être accéléré » constatent les auteurs de l’étude. Cependant, alors que les ETI sont convaincues par la transformation digitale, seule une entreprise sur cinq a débuté sa transformation et la grande majorité revendique un accompagnement renforcé, ce que confirment les chiffres de la Fédération internationale de la robotique. La France compte 154 robots pour 10 000 employés, là où l’Allemagne en a 338 et Singapour 831. « Malgré la progression sensible des investissements industriels, l’industrie française reste sous-équipée en robots. Certes, des projets ambitieux d’usine du futur voient le jour en France. Mais elle reste encore en surface du tissu industriel. Pour preuve, l’écart entre les 70 % de dirigeants de PME et d’ETI qui affirment que la modernisation de leur outil de production est un enjeu et les 10 % d’entreprises françaises qui ont effectivement intégré une application d’intelligence artificielle, soit deux fois moins qu’aux États-Unis. Face aux défis de la croissance, de l’emploi et de la localisation de la production industrielle sur nos territoires, nous n’avons pas le temps d’hésiter car le reste du monde ne nous attend pas. » avertit dans une tribune Agnès Pannier-Runacher, secrétaire d’État auprès du ministre de l’Économie et des Finances.
Un rythme d’investissement insuffisant
Le constat est à peu près identique du côté de l’Alliance Industrie du Futur, du Symop et du GIMELEC (le Groupement des entreprises de la filière électronumérique française) dans leur dernière étude “les leviers pour intégrer l’Industrie du Futur d’ici à 2025”. Selon cette enquête réalisée par Accenture Strategy auprès des dirigeants de 450 entreprises de plus de 50 salariés, le taux de croissance annuel de la robotisation plafonne à 3,4 % en France contre 6,7 % pour l’Espagne. En parts du stock mondial, la France stagne à 1,6 % contre 7,5 % pour l’Allemagne. Par ailleurs, la dépense en machines et équipements industriels est jusqu’à 3 ou 4 fois moins importante en France qu’en Italie et en Allemagne. Du côté du 4.0, seules 14 % des entreprises interrogées ont partiellement déployé une solution digitale « Industrie du Futur » et 2 % l’ont totalement déployée tandis que 81 % des entreprises ne connaissent pas ou ne développent pas les véhicules guidés autonomes (AGV). La conclusion est sans appel. Pour les protagonistes de l’étude, le rythme d’investissement dans l’industrie 4.0 est insuffisant à cause d’un déficit de formation et d’un manque d’accès aux compétences : il faut sensibiliser les industriels aux bénéfices du 4.0 et le grand public aux carrières industrielles.
S’appuyer sur les fondamentaux
Dans ce contexte, il faut rester solide pour ne pas miser sur le « tout technologique » pour accroître les performances, la qualité et le rythme des cadences dans un environnement sans cesse mouvant où la demande des consommateurs est en perpétuel changement. Car, cette quête technologique peut faire oublier à certains industriels “les fondamentaux”. Certes, les outils sont présents et la tentation est grande d’investir massive- ment mais, sans une réflexion globale, sans une refonte de l’organisation, une remise à plat des modes de management, un changement de culture d’entre- prise avec la prise de conscience que l’élément principal au cœur de la transformation est le facteur humain, l’enthousiasme risque souvent de céder la place aux désillusions. « L’IA, la blockchain, la robotique, la fabrication additive ne sont que l’aboutissement d’une démarche que doit mettre en œuvre l’entreprise avant de franchir le pas et de s’équiper en nouvelles technologies. Avant d’investir, il faut au préalable vérifier que tous les fondamentaux en matière d’organisation, de management, de Lean soient mis en place. Sans une phase de réflexion et d’idéation en amont pour imaginer la feuille de route à tenir, les industriels risquent des désillusions sur l’adoption des nouveaux outils et peuvent générer du stress au sein de leurs équipes » prévient Vincent de Bentzman, président de Techteam. Selon Julien Chevalier du cabinet Horenso, robotiser et digitaliser de manière systématique n’est pas non plus forcément la meilleure solution. « Beaucoup d’industriels font l’erreur de vouloir robotiser ou digitaliser à tout prix ou par dogmatisme. Or, il ne faut pas succomber aux fausses promesses de la digitalisation. Il faut tout d’abord faire un premier bilan à l’image de ce que l’on faisait il y a 50 ans. On va dans l’usine, on réfléchit en observant la situation et on résout le problème. Dans un grand nombre de cas, les industriels qui se précipitent vers les nouvelles technologies pour résoudre leurs problèmes, déchantent. Ils surinvestissent ou n’investissent pas du bon côté. » confirme le dirigeant.
Caractériser le problème pour mieux le résoudre
À titre d’exemple représentatif, Horenso est intervenu récemment dans une société du secteur aéronautique dans le cadre d’un projet d’industrialisation de nouveaux produits. « L’entreprise avait fait appel à un intégrateur et investi dans une chaîne composée de 23 robots dédiés à l’assemblage de pièces mécaniques et composites, à laquelle s’ajoutaient des applications qui faisaient discuter les robots entre eux. Sur cette ligne travaillaient en cadence 21 opérateurs. Le premier constat, que nous avons fait, est qu’il n’y avait pas de directives précises l’organisation à adopter sur cette ligne. Or une logique importante est à respecter sur les flux de process (de matériaux). Elle consiste à définir tout d’abord les flux les plus simples à mettre en œuvre. Une fois les flux validés, nous choisissons les moyens à investir en priorisant l’ergonomie et la qualité, et quel est le poste de travail qui doit être robotisé. Nous observons que dans 90 % des cas, les industriels raisonnent à l’envers et se demandent quels moyens de production ils vont acquérir avant de penser à travailler sur les flux physiques et informationnels. On achète une machine sur catalogue et on demande ensuite aux gens de s’adapter autour. C’est dans ce cas que l’on enregistre le plus de perte ». L’objectif de l’usine étant de réaliser 200 pièces mécaniques par jour alors qu’elle plafonnait à 70, Horenso et les équipes de l’usine se sont recentrés sur les bonnes pratiques du Lean Management qu’appliquent les entreprises industrielles les plus performantes. L’équipe a choisi de remplacer tous les robots sauf 2, au profit d’opérateurs en reconfigurant la ligne dans une approche globale « selon des concepts qui ont déjà fait leur preuve ». Au final, au lieu d’occuper une surface de 2 000 m² au sol, la ligne a été redéfinie dans un espace de 400 m² comprenant tous les équipements avec une meilleure optimisation des déplacements.
« Nous revendiquons ne rien avoir inventé. Nous utilisons des standards existants. Nous avons simplement utilisé les règles du Lean qui fonctionnent chez Toyota par exemple. Sur l’aspect flux, nous avons appliqué les standards observés dans l’automobile (Valeo, Faurecia). Concernant la maintenance, nous nous sommes inspirés des concepts du Japan Institute of Plant Maintenance (JIPM). Nous avons trop tendance à penser en termes de moyen alors qu’il faut avant tout caractériser le problème pour mieux le résoudre.
Publication originale : https://www.usinenouvelle.com/article/industrie-du-futur-difficile-de-ne-pas-ceder-au-4-0.N940821
Laisser un commentaire